Steel Plate & Sheet - Grades & Finishes
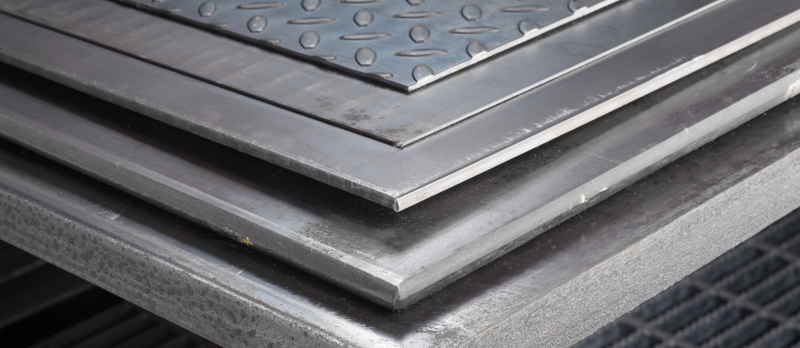
Grades
Carbon steel is an alloy of iron and carbon, often with other elements in small percentages that affect the properties of the final product.
A few of the most common grades of steel plates and sheets are:
- A36 - a low carbon steel with good strength, formability that can be securely welded with a minimum yield strength of 36,000 PSI
- A572-50 - higher strength steel with a minimum yield of 50,000 PSI and increased corrosion resistance
- A516-70 - steel with a minimum tensile strength of 70,000 PSI that is generally used in pressure vessels and boilers
- AR400 - abrasion resistant, quenched and tempered alloy steel with a high level of hardness, making it brittle and so it is not intended for structural applications
- A588 - also known as Corten, this steel weathers well, forming a stable rust-like appearance that eliminates the need for painting
- A1011 - a hot-rolled carbon steel alloy primarily used for sheets with high strength and formability
There are many other grades of steel plates and sheets with specialized properties. If you need it, we can get it!
Yield strength is the amount of force that can be withstood before permanent deformation. Tensile strength is the amount of force required to pull something (like a sheet of steel) to the point where it breaks.
Finishing and Treating
Steel sheets and plates are made by rolling a slab of steel through a series of rollers until the desired thickness and material properties are achieved. Each stage in the rolling and finishing process produces a salable sheet or plate with distinct finish and properties.
Hot Rolled Steel
This is the most common and simple finish and the first step to making steel plates and sheets. A steel slab is heated, typically to 1,700 degrees F, and passed through a series of rollers - each set of rollers making the slab thinner until the desired thickness is achieved. Then the steel is allowed to cool to room temperature and cut to size or rolled into large coils.
Hot rolled steel is the easiest and cheapest sheet steel to find. It is fairly ductile, and thinner sheets can be easily formed with hand tools. Its dimensions are less refined compared to cold rolled steel.
Pickled and Oiled
A roll or sheet of hot-rolled steel is dipped or passed through a pickling bath. A solution of very strong acid removes the scale and dirt from the sheet or plate, leaving the raw steel exposed. It is then passed or dipped in an oil bath to protect the raw steel from oxidation, which would begin immediately without protection, especially in humid environments.
Steel that has been pickled and oiled has the same material properties as straight hot rolled steel but is cleaner to work with and easier to clean for painting.
Cold Rolled Steel
Hot rolled steel sheets or plates, that have previously been pickled and oiled, are again run through a series of rollers without the addition of heat. This compression of the steel at room temperature causes it to become work hardened.
To produce the finished product, the steel is then annealed and tempered.
Annealed
Cold rolled sheet or plate is put into a furnace and heated to a temperature below the melting point of the material. The steel is removed from the furnace and allowed to cool to room temperature. When heated, the steel grain realigns and some of the effects of work hardening are diminished.
Temper Rolled
Annealed steel is passed through one more set of rollers. These rollers are primarily to refine the finish further and diminish slight deformities or warps in the steel.
Cold rolled steel is made to much tighter dimensional tolerances and the surface is more uniform and refined. Typically the edges are quite square. This steel is harder and stronger but won't hold shape as well as hot rolled steel when it is bent. It is less ductile and when bent, the deformed zones are more likely to spring back than to take the bend. Steel sheets or plates that make it to this stage are ideal when looks and strength are important.
Further Finishing
Specialized coatings can be applied to the surface of the steel via dipping or electroplating. Most commonly zinc is applied to the surface to produce what is known as galvanized steel. Learn more about the galvanizing process here.