Plasma Cutting OEM Parts
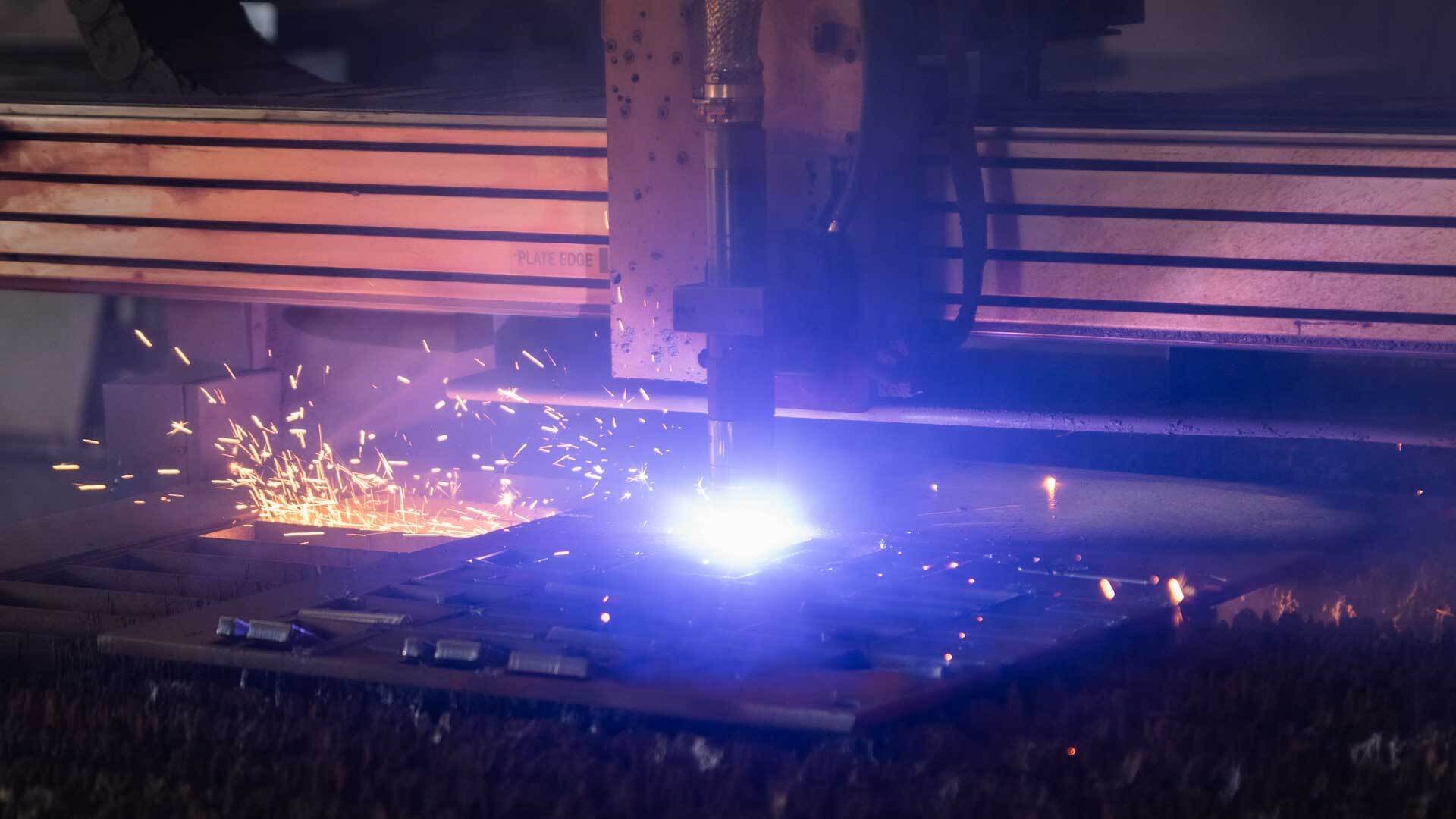
Plasma cutting is a versatile and efficient method for crafting OEM parts.
In the manufacturing landscape, Original Equipment Manufacturer (OEM) parts are the backbone of reliability and performance.
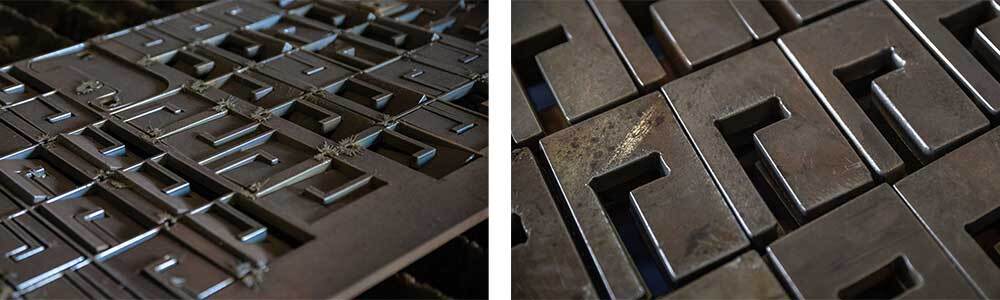
Our Process
Several steps are involved in initiating a plasma-cutting OEM project.
- First, we review the customer's requirements, including the material, the desired specifications, and specific design considerations.
- Next, we select the appropriate plasma-cutting consumables based on the material type, thickness, and desired cut quality. Once the equipment is set up and calibrated, the cutting process begins, with the plasma torch following the programmed path.
- Quality control measures occur throughout the process.
- Finally, we package and ship the finished parts.
Advantages for Manufacturers
Manufacturers stand to benefit significantly from utilizing plasma-cut OEM parts in their production processes:
- Enhanced Precision and Quality: Plasma cutting offers cost-effective precision, enabling manufacturers to produce parts with complex geometries and tight tolerances.
- Improved Efficiency and Productivity: Plasma cutting offers fast cutting speeds and minimal setup time, which reduces lead times.
- Cost-Effective Solutions: Plasma-cut OEM parts offer cost-effective solutions for manufacturers, optimizing material usage and minimizing waste.
- Customization and Flexibility: Plasma cutting allows for the customization of OEM parts to meet specific requirements, ensuring compatibility and seamless integration.
YouTube
Subscribe to our YouTube Channel to see our Plasma Cutting machines in action!
Helpful Links
Categories: Value-Added Projects